Methods of Quality Assurance Certification, Six Sigma, and Lean Principles
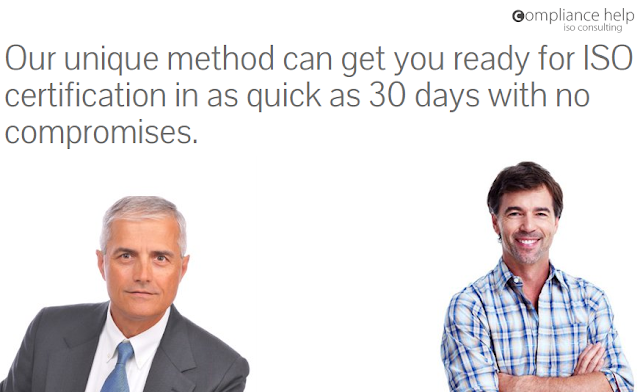
Quality assurance methods cover the quality issues that are often seen in the products or services offered by a business. Lean and Six Sigma principles include several approaches and metrics to progress a process meant for promoting the efficiency of a business. These approaches can remove the defects and meet the flaws of the organization. These days, the companies should use a quality assurance approach, lean and six sigma principles together in a more generalized way. A combination of these approaches can help the organizations offer high-quality products or services with minimal defects in the best possible way.
In this blog, we will discuss quality assurance certification, lean principles, and Six Sigma principles one by one.
Quality Assurance
Quality assurance methods define what functions a product or service must fulfill and which characteristics it must contain. They should be specific when defining the required resources. Apart from these, they should ensure that these resources are easily available in the industry. So far, production is concerned; an organization must specify which characteristics are required for incoming materials and supplies. It is also important to state the qualifications of the employees who are assigned to carrying out the process and the tests required to verify actual and the particular parameters. In this way, a business can receive the expected results in the final output.
Lean Principles
Several organizations employ lean principles to enhance their efficiency. They continuously monitor the production processes to decrease waste and unnecessary efforts. This is vital especially for the small enterprises that have a limited resource capability. Lean principles figure out and remove process steps that fail to add value, track movement of employees and materials without any constructive purpose, and repeat mistakes that are quite time-consuming. They tend to reduce waiting time to streamline the process and emphasize the on-time delivery. Most of the organizations implement these principles by allotting specific tasks for performance. Their ultimate aim is meeting the desired outcomes. Therefore, individuals are assigned for these several tasks. The organizations provide them with leeway in determining how to achieve the expected outcomes. Lean principles help the small businesses gain quality assurance certification.
Six Sigma Principles
Six Sigma principles insist on reducing the errors. The term implies that a statistical value (stands for almost zero flaws) should be achieved. Measuring the defects is an integral part of the entire quality management system. An error stands for an output that doesn’t meet the customer expectations. Organizations design several simple processes can assure quality products or services with low defects. These simple production processes are vital for small entrepreneurs as it allows the personnel for several business functions. An insight into the functions can explain the five functions of definition, measurement, analysis, improvement, and control. Several organizations use these functions to simplify their existing production processes and assess how successful they have become in producing products or services with zero defects. You can ask reputed ISO certification services to conduct this assessment on behalf of your company.
A Final Takeaway
Do you know what the key to an organization’s performance is? The secret key to success lies in the accomplishment of goals that help to fulfill the ultimate motif of a business. Quality assurance methods offer output that helps to meet quality goals. In this context, it is important to note that they do not help a business increase the production efficiency. Use of lean principles allows the companies to maintain a high-level that they need while growing and developing. Six Sigma principles support quality assurance system and lean principles by regulating statistical measurements into the business operations. If your organization combines quality assurance together with six sigma principles and lean principles, you will be able to reduce the cost and extra expenses, improve the performance of your business, and deliver higher quality products or services.
Once the quality improvement plan (a blend of quality assurance strategy, lean principles, and Six Sigma) is drafted and executed properly, you will be able to explore excellent benefits of quality assurance management. Many reputed companies have witnessed success by blending these three approaches together. Today, they are being considered as the industry giants. Therefore, you too should follow this strategy to assure your success.
To know more, do follow the upcoming blogs!
Comments
Post a Comment